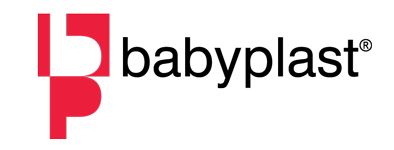
Babyplast Saves you money, and Lots Of it!
Babyplast is one of the smallest, fully hydraulic micro injection molding machines available. It’s the ideal machine for the production of micro parts from all types of thermoplastic materials up to 420o C, plus metals (MIM), ceramic (CIM), and wax. If you need to produce a part that weighs from 0.01g to a maximum of 15g, we have a real winner as an alternative the BABYPLAST micro-injection molding machine.
Babyplast is mainly used in technical fields: Electronics – automotive – micro-mechanics – medical – furniture, but it is also used by manufacturers of toys – promotional products – cosmetics – costume jewelry. The majority of the molds developed for Babyplast are not for preliminary production or prototypes, but for full production.

How Do You Save Money With Babyplast?
- The initial cost of Babyplast machines is a small fraction of that of large machines that are simply overkill for many applications.
- Babyplast running costs are much lower, as the maximum power supply needed is only 3.5Kw. ($2.00 to $2.65 per hour, including amortization of the machine over 5 years).
- Babyplast makes possible reduced sprue size and residence time. This is particularly advantageous when molding expensive technical thermo plastics.
- Mold construction for use with Babyplast is less expensive, because you only need to make the cavity plate.
- Mold change is very quick, taking only 3 to 5 minutes, resulting in savings in labor costs and machine down time.
- Because of these savings, you don’t need to make more expensive molds with a large number of cavities, and then use them in long production runs to amortize the cost of the mold, mold change time, power, etc.
- Molds for use with Babyplast have a relatively smaller number of cavities, which is an advantage when you have rejected parts due to a damaged cavity, and you do not notice the problem for some period of time. With a mold that has many cavities, you must check a large container of parts, and stop the whole production. If a Babyplast mold has a damaged cavity you check a much smaller container of parts. And if you have multiple Babyplasts with the same molds, and one is giving you defective parts due to a damaged cavity, you only have to stop one machine while continuing production with the others.
- Babyplast is user friendly, and do-it-yourself maintenance is very easy for customers. This reduces repair costs and machine down time considerably. And, of course, expert telephone and e-mail support is available as needed from ALBA.
- Babyplast spare parts cost less than those for large machines. For example, if a Babyplast injection piston and chamber needs to be changed, the parts will cost only about $500, and the work can be done by the customer in 30 minutes. How much does a screw cost on a standard machine and how much would it cost in labor to replace it?
The Dollar Savings Sound Good! But What About Quality?
Molds used in the production of precision parts normally have a small number of cavities even on traditional machines. Babyplast molds naturally have a small number of cavities.
Babyplast can process all thermoplastic materials up to 420o C, plus ceramic and metal sinter, and wax. Parts produced on Babyplast containing GF are mechanically better quality because Babyplast uses a piston that does not break the fibers as often happens with screw systems.
With more than 10,000 applications used on the Babyplast machine, that include the use of the most varied thermoplastics, various types of molds, we are able to put at the disposal of the customer our experience, that has no equal in the field of micro injection molding.